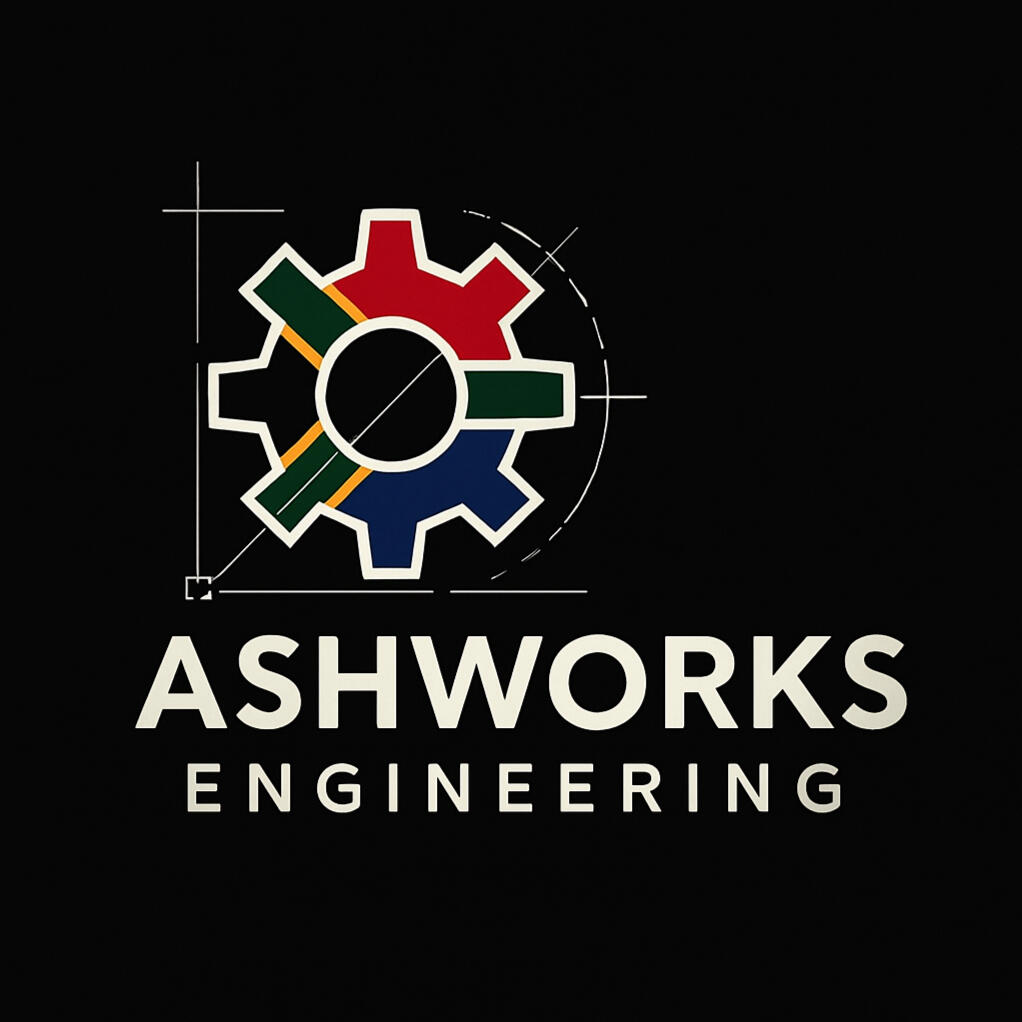
Precision CAD and engineering for builders, restorers, and race teams. From scan to part in as little as 4 weeks. Delivered globally.
AshWorks Engineering delivers specialist CAD and re-engineering services for builders, restorers, and EV innovators worldwide. From hand-drawn sketches to 3D scans, we create and coordinate custom parts with rapid turnaround—so you can build without compromise.
Got a tricky part or big idea? Let’s build it.
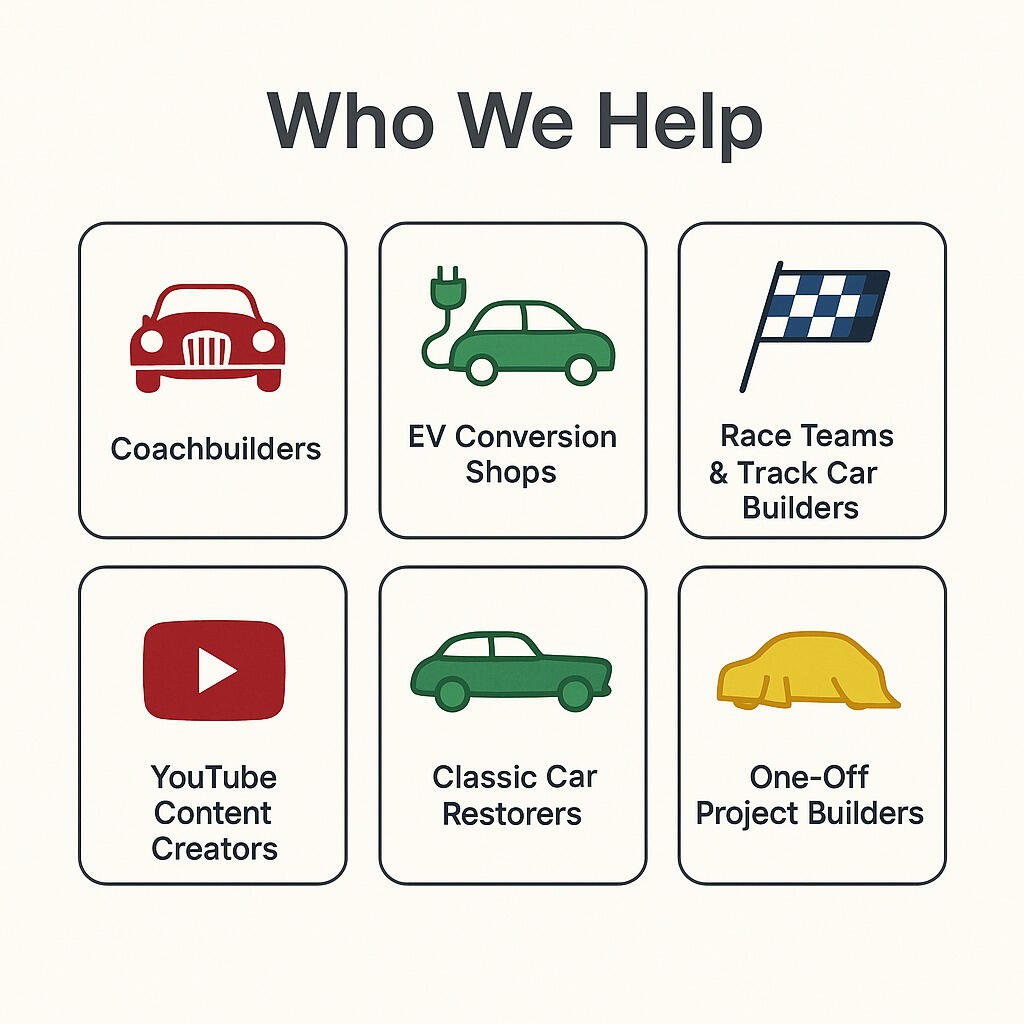
“I’d been stuck trying to source a part that no longer existed, and every workaround felt like a compromise. Ash didn’t just replicate it—he improved it. He walked me through the process, showed me the CAD, and had the finished part in my hands within weeks. Proper engineering, done right."
— Client, Vintage Supercar Owner
About Ash Venter (Founder)
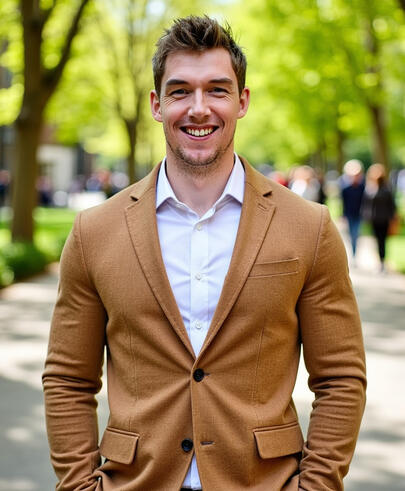
Originally from South Africa, I moved to the UK at 19 to pursue a career in automotive and mechanical engineering.I began my career as a graduate at SMC Design, where I spent 8 years developing advanced jigs, fixtures, and Body-in-White (BIW) tooling. I worked on tooling and hemming systems for OEMs like BMW, JLR, Mercedes, and Ford.
Toward the end of my time there, I was leading key projects and built a full training program for new engineers to help them hit the ground running—a system that’s still in use today.I then moved to McLaren Automotive, where I had the privilege of working on some of their most innovative vehicles, including:
W1 – Full interior development from early concept to final production, across ergonomics and seating to HVAC, cluster design, and rear luggage packaging
Solus GT – Assisted Ergonomic layout, seating position
Elva, 765LT, P17 (720S replacement) – handling everything from thermal packaging to underfloor aero, luggage zones, and bumper assemblies
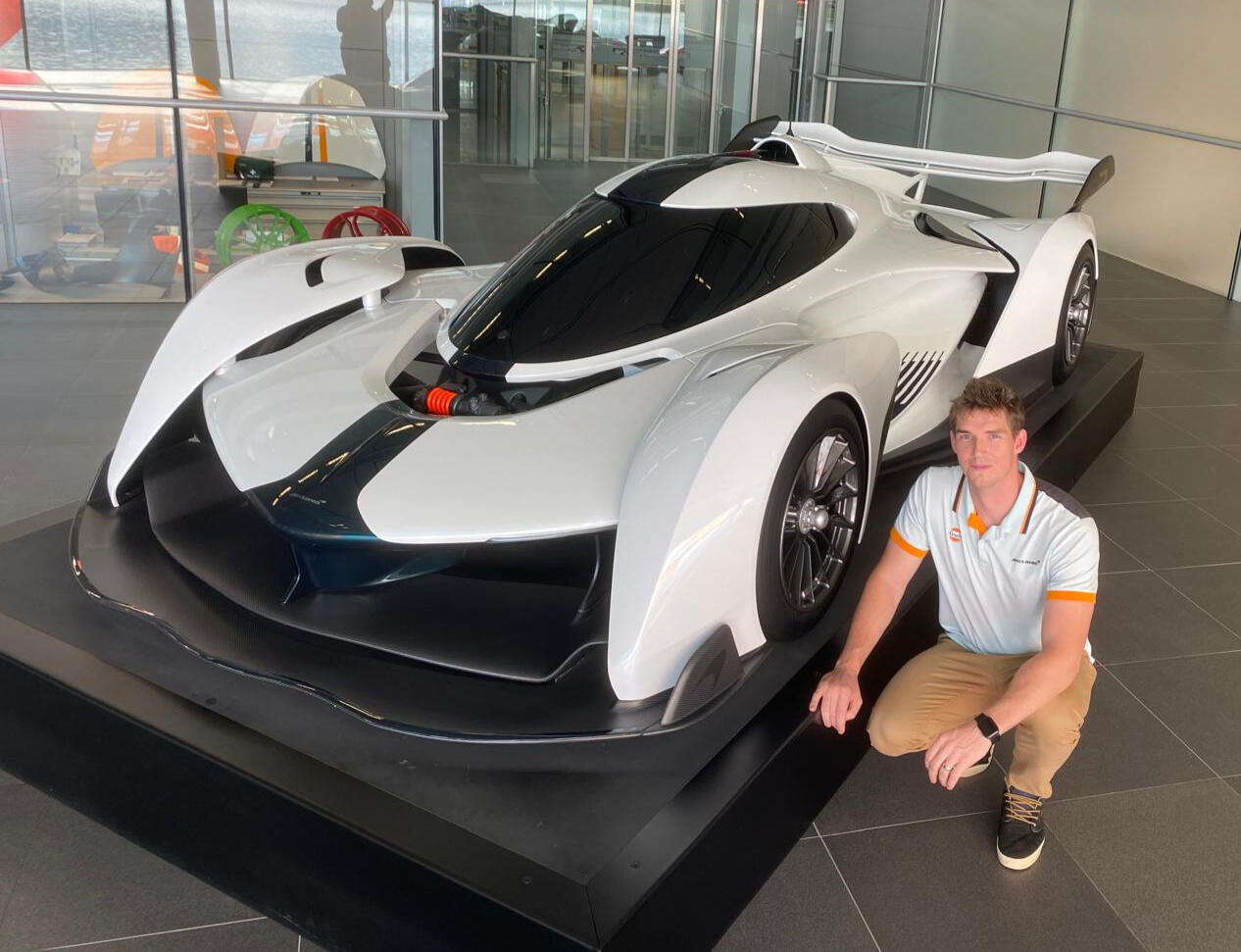
Solus GT at McLaren HQ
"I worked with Ash for several months. We had regular conversations and meetings in order to solve various problems of design, manufacture and production. He was always professional, listening and contributing in equal measure, focussed on improving the product, never accepting second best, and always with good humour. Not just a great designer but a good person too."
Andrew Briggs, Manufacturing Engineer (Fablink)
After McLaren, I took on a leadership role as Head of Mechanical Engineering at Moke International. There, I was responsible for improving chassis design, reducing build time, and managing a cross-functional team across design and production. I oversaw the rollout of new SOPs, reworked key parts for better manufacturability, and transitioned chassis production to a new supplier—while driving down the bill of materials and improving production flow.
At Moke, I wasn’t just designing—I was solving problems in real-time, on the floor, making changes that impacted build speed, cost, and quality. That hands-on, full-lifecycle experience sharpened my belief in lean, intelligent engineering.My colleagues often described me as the "go-to problem solver”—the one who could find solutions when things got stuck. Whether it was a cooling system that didn’t function right, or a part that just wouldn’t package properly, I’ve always enjoyed untangling complex problems and turning them into clean, parametric CAD models that are easy to adapt, test, and build.
"Working with Ash has been a game changer. His exceptional problem solving skills consistently streamline complex design challenges, resulting in efficient and innovative solutions. Ashley brings a combination of technical expertise and pragmatic real-world thinking that elevates engineering output. His attention to detail, speed of thinking, and ability to see the bigger picture make him an invaluable part of any project."David Moore - Vehicle Project Manager (Moke Int)
Need a part designed and delivered quickly? We manage the complete process, turning your sketches into engineered reality.
Process Showcase
At Ashworks Automotive, we follow a proven process to ensure efficient and high-quality results for every project. The following examples illustrate our approach to solving common automotive engineering challenges, demonstrating our commitment to precision, collaboration, and delivering exceptional outcomes.
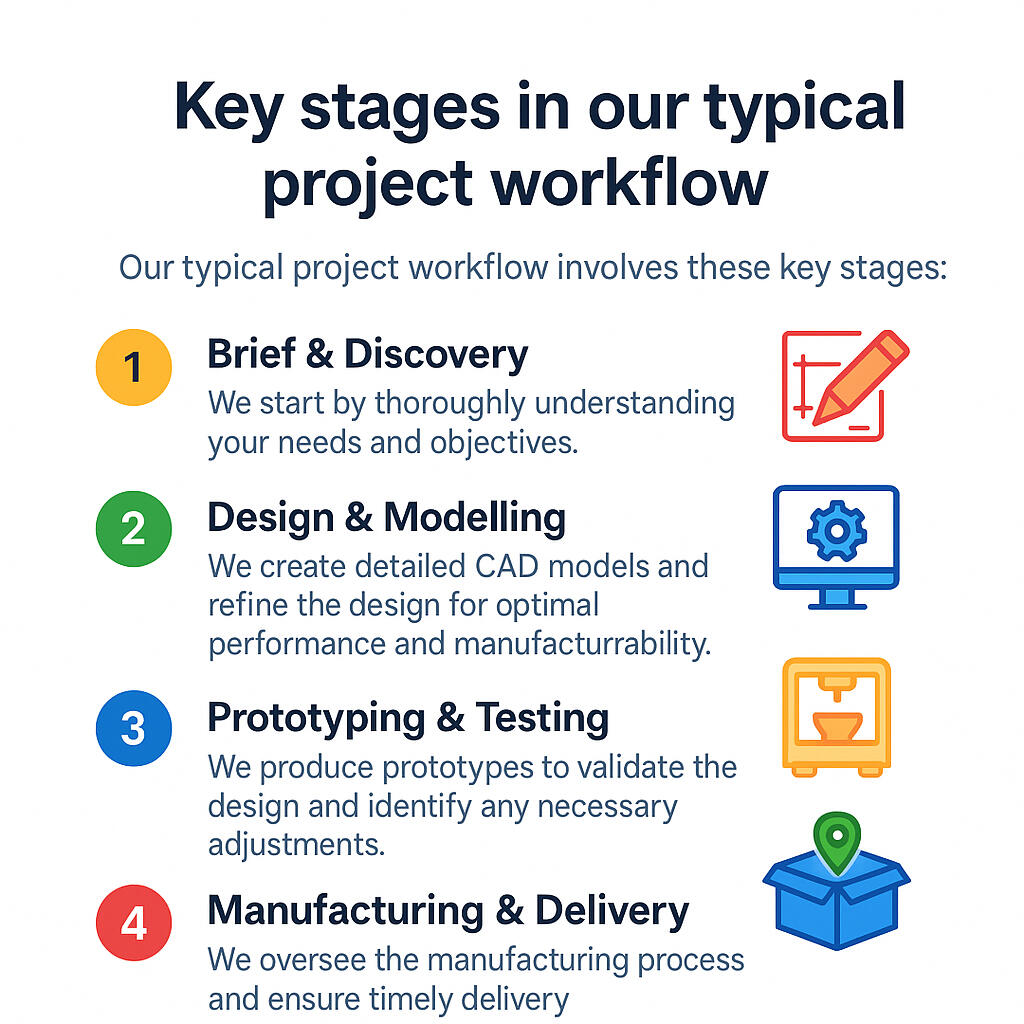
"Working with Ash has been an outstanding experience. He brings a rare combination of technical precision, creativity, and deep automotive knowledge. His ability to turn complex ideas into detailed, functional designs is truly impressive.
He’s not only skilled, but also a great communicator and collaborator, approaching challenges with a clear mind and a solutions-focused attitude."Matt Newman - Head Of Supply Chain & Purchasing (Moke Int)
Example project 1 - Designing a supercar radiator mount
In this example, our client needed a replacement part for a well-known vintage supercar—specifically, a low-temperature radiator mount that was no longer available on the market. With a tight deadline and no off-the-shelf solutions, we stepped in to re-engineer the part for performance, fit, and fast turnaround. This case highlights our full process: from brief to delivered component.
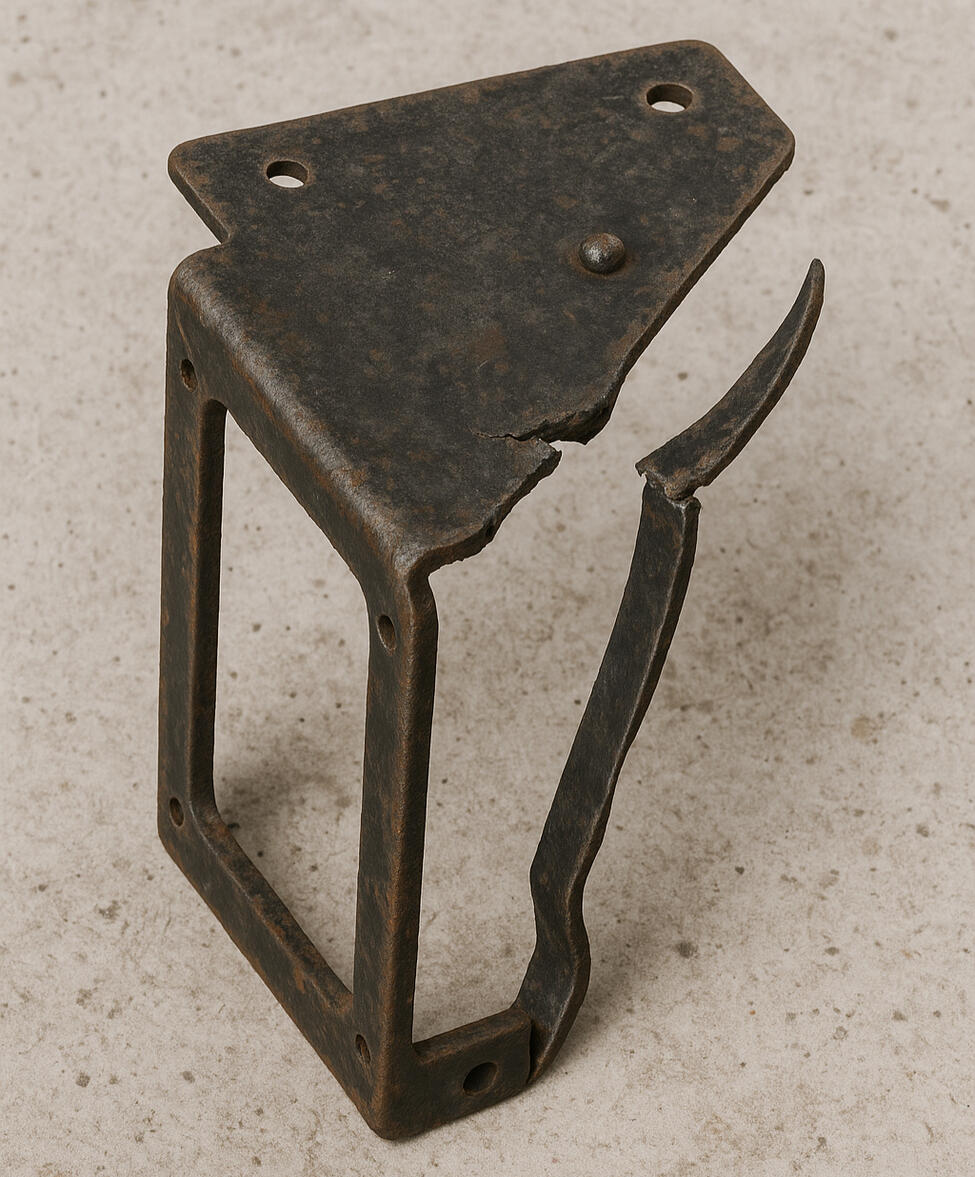
Client's broken part
1. Brief & Requirements Gathering
We began by working closely with the client to clearly define the project’s goals and technical requirements. This included understanding performance expectations, material preferences, and any constraints such as tight packaging space, mounting interfaces, and integration with the existing cooling system. Through collaborative discussions, preliminary sketches, and precise part measurements, we developed a full understanding of the original design. Where required, we reverse-engineered from damaged components to ensure dimensional accuracy and functionality in the new solution.
2. Design & Modelling
With the brief defined, we moved into CAD development. Using precision measurements and reference geometry from the original part, we created a fully parametric 3D model of the radiator mount. The design was refined for strength, durability, and ease of manufacture—taking into account material behaviour under thermal loads and integration with the vehicle’s existing architecture. Multiple design iterations were reviewed with the client to ensure every detail aligned with the brief.
Images of : 3D Part & Final Manufactured Part
3. Prototyping & Testing
To validate the fit and function of the new design, we produced a prototype using FDM 3D printing. This allowed for a hands-on test fitting within the engine bay and confirmed clearance, alignment, and attachment points before committing to final manufacture. Feedback from the client was incorporated at this stage, with minor adjustments made to bolt spacing and reinforcement ribs for added rigidity.
4. Manufacturing & Delivery
Once approved, the final design was manufactured through one of our trusted low-volume suppliers, using a lightweight, heat-resistant composite suitable for the cooling system environment. AshWorks handled all manufacturing liaison, quality control, and logistics. The finished component was delivered to the client within 4 weeks of the initial brief—ready to fit, tested, and performance-ready.
“I’d been stuck trying to source a part that no longer existed, and every workaround felt like a compromise. Ash didn’t just replicate it—he improved it. He walked me through the process, showed me the CAD, and had the finished part in my hands within weeks. Proper engineering, done right."
— Client, Vintage Supercar Owner
Stuck with a difficult part design? We specialize in transforming your rough ideas into fully engineered, production-ready components.
Example project 2 - High-Performance Brake Cooling Ducts
In this project, our client was building a high-performance car on an existing platform and required custom-designed front brake cooling ducts. Off-the-shelf solutions didn’t offer the performance, weight savings, or fit required for their specific setup. We were tasked with creating a lightweight, aerodynamically efficient ducting system to deliver focused airflow to the brakes under track conditions—while integrating seamlessly with the existing suspension geometry and bodywork.
1. Brief & Requirements Gathering
We started by working with the client to understand the cooling demands of the upgraded brake system, the physical packaging constraints of the vehicle’s front end, and the aerodynamic targets for the ducts. Mounting points, airflow paths, and duct length were all discussed. We gathered input from the client's suspension and brake setup and received reference data from the wheel arch area to begin the design process. The brief was clear: deliver high performance, low weight, and a professional fit and finish—fast.
2. Design and Modelling
Using the packaging envelope provided, we developed a 3D CAD model for a two-piece duct system designed for easy installation and directional airflow efficiency. Parametric modelling allowed for iterative shape tuning, focusing on reducing pressure drop and ensuring direct airflow to the brake disc. The design was optimized for composite production, including flanges and fixings for straightforward fitment onto existing mounting points.
Images of : Surface Model, 3D Part & Final Manufactured Part
3. Prototyping & Testing
A first prototype was created using lightweight PLA 3D printing to test fit and airflow clearance. After a successful dry fit, we simulated airflow through the duct in CAD to validate the shape under real-world speed conditions. The client provided in-situ feedback from mock track positioning, which led to minor design refinements for improved hose clearance during full suspension travel.
4. Manufacturing & Delivery
The final design was produced in a lightweight, high-temp-resistant carbon composite through our trusted manufacturing partner. The surface finish was pre-preg quality, and the parts were shipped with all mounting hardware included. From concept to delivery, the entire process was completed successfully ready for installation and testing at the track.
"Look, I could’ve bodged something with duct tape and prayers—but I wanted it done properly. Ash came in clutch with custom ducts that fit like OEM, flow like a jet engine, and actually work. He even turned it around in record time. This is the kind of nerdy engineering I love. Definitely going in the next video—subtle flex included."
— Client, YouTuber
Our Services
AshWorks Engineering provides specialist CAD and reverse engineering services tailored for custom automotive projects, EV conversions, and classic restorations. Whether you're starting from a 3D scan, a rough sketch, or a broken part, we turn ideas into production-ready solutions.
We offer a full-service path from concept to manufactured component. Whether it’s one part or a full system, AshWorks handles the engineering and production—so you can stay focused on the build.
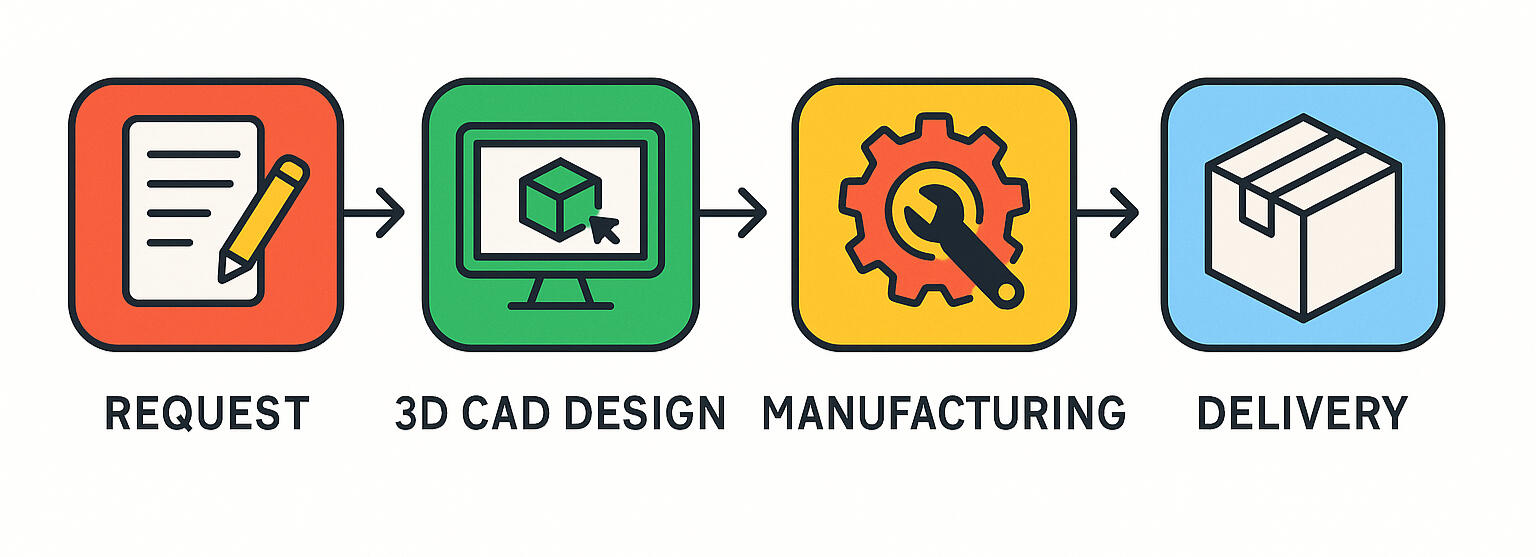
Our core services include:
🧠 Engineering & Design
3D CAD modelling
Transforming your concepts into precise digital models.
Ashworks Automotive offers expert 3D CAD modelling services, creating detailed and accurate designs for individual components, assemblies, and full automotive systems.
Whether you have a sketch, a concept, or a problem to solve, we use industry-leading software (SolidWorks, CATIA V5 & V6) to deliver models optimized for design visualization, simulation, and manufacturing.
Prices start from £250
Reverse engineering of damaged/missing parts
Do you have a physical part but lack the design files?
Our reverse engineering service accurately captures the dimensions and geometry of existing components using 3D scanning and measurement techniques.
We then create a fully parametric 3D CAD model, enabling you to reproduce parts, modify designs, or integrate them into new projects.
Ideal for classic car restoration, where original parts may be scarce, or for analyzing and improving existing designs.
Prices start from £500
Tooling, jig, and fixture design
Designing the tools that enable efficient manufacturing.
Ashworks Automotive provides design services for specialized tooling and jigs required for automotive production.
From fixtures for assembly to molds for composite parts, we create precise and durable tooling solutions that streamline manufacturing processes, ensure quality control, and improve production output.
Prices start from £350
Got a design puzzle that's hard to crack? From your first sketch to the final component, we'll engineer a solution and deliver it fast.
⚡EV & Thermal Systems
Cooling layout and airflow packaging
Optimizing thermal performance for demanding automotive applications.
Ashworks Automotive offers expert design and packaging of thermal and cooling systems.
We ensure efficient heat dissipation and temperature management for critical components, considering factors such as airflow, space constraints, and operating conditions.
This is crucial for high-performance vehicles and EV applications to maintain optimal performance and reliability.
Prices start from £1,000
EV component design and mountings
Need to fit EV gear where it was never meant to go?
I’ll help you package electric drivetrains, batteries, and controllers into classic or custom builds—without compromise.
I design precise, lightweight mounts and structural supports that integrate cleanly with your existing chassis, making the install safe, efficient, and road-ready.
Pricing: From £850
Carbon fibre part upgrades
Upgrade tired plastic components with precision-engineered carbon fibre replacements.
Whether it’s a custom dash, center console, interior trim, or bonnet scoop, I reverse-engineer original parts and reimagine them in carbon for better looks, durability, and performance.
Perfect fit. Modern finish. No guesswork.
Pricing: From £350 per part
From your vision to a tangible part, delivered swiftly. We handle the entire engineering process, from concept to finished product.
📦 Delivery & Manufacture
Design for Multi-Material Manufacturing: 3D printing, and production with steel, aluminum, plastics, and carbon fiber
Low-volume production
Delivered to your door/workshop
Got a tricky part for a classic restoration, a complex custom build, or a novel EV conversion? We'll take your concept from napkin sketch to engineered, delivered part—fast.
Why Ashworks Engineering?
Ashworks exists to bring that same level of technical expertise to custom builders, classic restorers, coachbuilders, and performance-focused workshops—people who need smart, efficient design and engineering, without the OEM red tape.I work closely with clients to take their ideas, rough sketches, or even physical parts and turn them into real, manufacturable components. I manage the entire process—from concept and CAD design to prototyping and manufacturing—using trusted partners in both the UK and overseas. The result: precision parts, delivered globally.Whether you’re restoring a one-off classic, converting a vehicle to EV, or reimagining a new component that doesn’t exist yet—I can help you bring it to life.Everything I do is informed by real experience—from factory tooling at SMC, to cutting-edge design at McLaren, to production problem-solving at Moke.
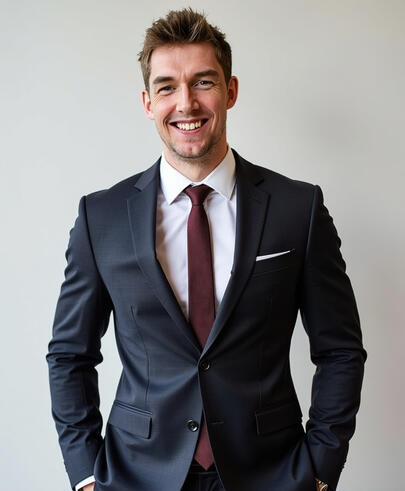
Contact
Have a project in mind, a part that needs reverse engineering, or just want to chat through an idea? Whether you're building something new, restoring something rare, or solving a tricky design challenge—AshWorks Engineering is here to help. Reach out directly via email or phone. We work with clients across the UK and globally, and aim to respond to all enquiries within 24 hours.
Tel: 07398643165
Email: [email protected]

"Ash and I worked extensively on a vehicle project at McLaren, where he consistently demonstrated his tenacity, diligence, and strong work ethic. He showcased both pragmatism and empathy in understanding various attributes, systems, and functions of the vehicle. His attention to detail and ability to address challenges effectively make him a standout engineer. Ash is also a creative thinker bringing fresh, innovative ideas. I would trust him to lead any project, improving processes and driving success."Oliver Bray - Senior Design Engineering Lead (McLaren Automotive)
Privacy Policy
Effective Date: 24/4/25AshWorks Engineering (“we”, “us”, or “our”) respects your privacy and is committed to protecting your personal data. This policy outlines how we collect, use, and safeguard your information.1. Information We Collect
We may collect the following information when you use our website or submit a form:
Name
Email address
Phone number (if provided)
Project information or enquiry details
2. How We Use Your Information
We collect your information to:
Respond to your enquiries or quote requests
Provide you with engineering services
Improve our website and client experience
Send follow-up messages where relevant
3. Sharing Your Information
We do not sell, rent, or share your personal data with third parties, except:When required by law
When using trusted service providers (e.g. email or hosting platforms) who process data on our behalf under strict privacy agreements
4. Data Storage
Your data is securely stored through our website provider and email systems. We retain enquiry information only as long as needed for business or legal purposes.
5. Your Rights
Under GDPR, you have the right to:
Access the personal data we hold about you
Request correction or deletion of your data
Withdraw your consent at any time
To request this, email us at [email protected].
6. Cookies
We may use cookies to analyse website traffic and improve functionality. You can control or disable cookies through your browser settings.
7. Contact Us
If you have any questions about this policy or how your data is handled, please contact:AshWorks Engineering
📧 [email protected]
📍 United Kingdom